
Cutters should be resharpened at appropriate intervals in order to ensure clean cut edges free from burnishing or fibre tear. Cutting and clearance angles should be maintained at each sharpening to prolong the life of the cutters. Cutters should be ground on the face only to minimise a reduction in cutting diameter. Carbide tipped tools should be rough ground with a 100 diamond grit wheel and then polished with a 400-600 wheel to increase cutter life by improving chip removal and reducing resin build up.
The time for resharpening can be estimated approximately by periodic examination of the cut edges. A more positive method requires the measurement of electric current to the drive motor. Assuming that the operating current with a new tool fitted is 100%, resharpening can be scheduled when the current increases by a predetermined amount, usually in the range 110 to 120%.
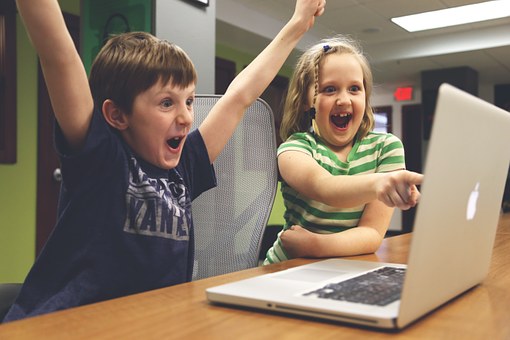
At lower feed speeds, the cutters will compress and abrade the MDF edges. The resulting high pressure on the tips and the increased temperature due to frictional heating will reduce the life of the cutters between sharpenings. At higher speeds, the greater spacing between cutter marks will increase surface roughness necessitating greater sanding effort to achieve the required level of smoothness before finishing.
Designs requiring heavy stock removal or intricate profiling may require a preliminary rough cutting or hogging operation followed by a second cut to achieve a smooth surface.