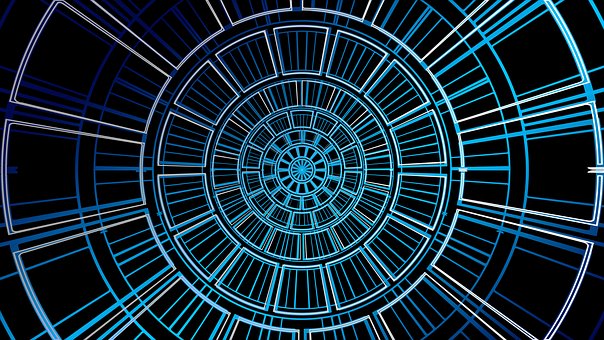
The dust produced when machining MDF is finer and more readily dispersed into the surrounding air than the dust from solid wood or particleboard. in this respect, MDF machining dust is similar to the dust produced when sanding finely textured hardwoods, both requiring a higher level of extraction efficiency. In particular, a minimum capture velocity of 20 to 30 m/sec is required at the dust generation point compared with 10 to 20 m/sec recommended for normal wood dust. The air velocity in the ducting should be in the range 15 to 20 m/sec to prevent an accumulation of dust (plugging) which could create a fire risk.

Meeting these requirements does not necessarily involve the installation of new extraction equipment for companies changing over from wood or particleboard to MDF. Experience has indicated that effective extraction of the MDF dust can be achieved in most instances by reducing the size of the collector hood openings and placing them as close as practicable to the point of dust generation.
Collection efficiency will also be improved by closing off ducts connected to machines which are not in use subject to maintaining the recommended minimum air velocity in the remaining ducting. In small and medium size companies, individual extraction units fitted to each machine have been found to be cost effective. CNC machines, which by the nature of their operation, generate large volumes of dust, are normally fitted with a brush collection head to limit the spread of dust and a high efficiency extraction system.
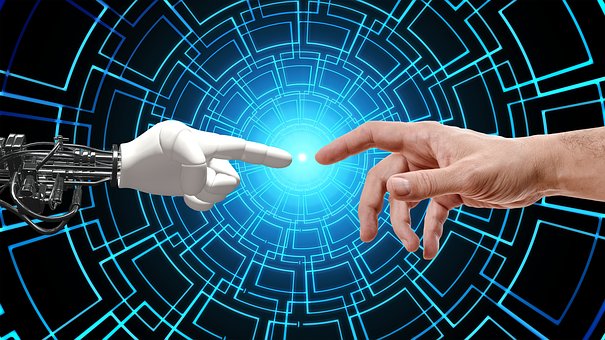